When we hear the term "service," we immediately think of repair or maintenance work. Yet nowadays, service involves much more than just repairs. In times in which production processes are becoming ever more complex, services must be all the more comprehensive, and cover every phase in the system life cycle.
In this day and age, production processes are becoming ever more complex. As a direct consequence, the corresponding services are also required to grow and adapt to this development. Individual service packages are required, which cover the complete system life cycle: from the orientation phase to the usage and modernization of your machines and systems.
This is where we come in: We want to support you and provide you with the services that you need at the current time and that offer you the most assistance. This may involve personal support for the project planning and configuration during your planning and engineering phase or perhaps a comprehensive repair service including collection of the components during the usage phase, when things are particularly urgent.
With our scalable services, we offer tailored solutions from a single source, thereby meeting your own individual requirements throughout the entire system life cycle.
The video is loading...
Bernd Rüdinger, Head of Service Mechanics / Mechatronics about the Life Cycle Service from SEW-EURODRIVE
For more details on the services we offer, come and see us at HANNOVER MESSE.
Come and visit us – for information and more!
Your benefits
-
Safety
You receive rapid, reliable assistance to guarantee the safety of your production process. -
Everything from a single source
You receive all services from a single source, closely meshed with our product portfolio. -
Expertise and advice
You can trust in over 85 years of expertise in the field of drive and automation technology and benefit from individual consulting. -
A single contact person
We are at your side and fully committed, wherever you are in Germany.
In which phases can you benefit from our support?
ORIENTATION
Before you invest in new systems, components and services, you require a comprehensive overview tailored to your situation: What is available? What rules and regulations must be observed? What trends and innovations should be considered? What is the right package for my requirements? We will provide you with helpful information to assist you in your orientation and decision-making.
Optimum services in this phase:
Personal consulting on
- Current & future trends – for your forward planning. We have our finger on the pulse and shine a light on current and future developments in drive and automation technology.
- Rules & regulations – to ensure you keep an overview of standards and legal requirements, e.g. in terms of safety technology, explosion protection and energy efficiency.
- Application & industry expertise – because we are happy to share our experiences from a whole range of industry sectors and applications from all over the world.
- Knowledge transfer – because as your good partner, we are happy to provide information and trends from a number of associations, including the German Engineering Federation (VDMA) and the German Electrical and Electronic Manufacturers’ Association (Zentralverband Elektrotechnik- und Elektronikindustrie, ZVEI).
- Information sharing at innovation level – our sales and product engineers will be happy to discuss your requirements with you personally. If necessary, we will also involve our research and development experts.
PLANNING & ENGINEERING
We will provide you with optimum planning – before you place an order. You will be supported by technical experts who have an in-depth understanding of your industry and applications. With 41 sales and service locations throughout Germany, we can offer you personal assistance and answer all your project planning and engineering questions. Or we can provide tips on how you can save maintenance and upkeep costs during the later usage of your systems.
Helpful "planning and engineering tools" are available for you to use at your workplace.
Optimum services in this phase:
- Concept development – to determine your needs. Tailor-made concepts for your drive, automation and safety technology, for example using performance specifications for programming applications or defining specific installation and drive safety concepts.
- Project planning & design – for selecting and configuring your drive components. Project planning for complex drive systems with particular attention to safety and energy requirements, plus all technical information and CAD data at the press of a button.
- Engineering – for modernization measures, planning new systems and implementing MAXOLUTION® system solutions. Good partners support you all the way from control cabinet planning, creating wiring diagrams and mechanical modifications during modernization all the way to project-specific software adjustments, system simulations and complete project management.
- Maintenance & operating concepts – for early development of customer-specific maintenance and operating concepts in the operation phase. This lays the groundwork for reduced and optimized storage, operation and maintenance costs and maximum system availability.
- Training – ensures you make practical progress. We make our drive technology expertise available through SEW-EURODRIVE’s training institute, the DriveAcademy®.
- Variant management – for standardizing and reducing product variants and simplifying master data management. Comprehensive advice about technical details and filter opportunities in our central database.
PROCUREMENT & DELIVERY
During the procurement process, you will benefit from outstanding process efficiency and consulting services. We are available to you with our expertise and will support you in, for example, increasing the speed and quality of your inquiry and order processing and ensuring smooth logistical processes. We provide personal advice, tailored to you. Be it electronic order management (EDI) or intelligent material flow – you decide what is the right service for you.
Optimum services in this phase:
- Electronic data interchange (EDI) – to support your entire order management process electronically, including ordering, electronic order confirmation, dispatch notification and invoice. We advise you on platforms such as MyOpenFactory, Basware and Seeburger AG or direct links to standard formats such as EDIFACT or XML.
- Delivery service – everything you wish for. We can provide standard or express shipping, direct courier delivery to the construction site, or even specific packaging requests.
- Electronic dispatch notification – a notification of dispatch that issues an immediate message as soon as your delivery leaves our premises. This keeps you in the picture and enables you to take the necessary steps. As a result, you benefit from optimized resource planning, precise control of production planning and speedy goods receipt processes.
- Barcode-Labels (DriveTag) – DriveTags are functional barcode labels that are attached to products or packages. You define the data they contain, which might include the SEW serial number and your material or project number to ensure efficient product identification and assignment of products at every process step – from receipt of goods, through storage and on to the downstream stages.
- Electronic billing – for rapid availability of your invoices by e-mail with additional XML invoice file or by EDI. This optimizes your processing of incoming invoices and administrative processes, and is also more environmentally friendly.
INSTALLATION & STARTUP
Would you like to avoid errors during the installation and startup phase? Do you want to safeguard the functionality of your system with an inspected installation of the drive technology? Would you like to optimize your machine and system processes by means of customized, application-specific programming? Do you want to reduce costs and avoid consequential damage by obtaining professional startup support? Our experienced service experts and engineers will be happy to assist you.
Optimum services in this phase:
- Installation consulting – for the correct mechanical and electrical installation of your drive technology. With our project experience, you can shorten installation times and safeguard your system functionality. We are happy to provide support at every step, from inspecting the mechanical and electrical installation to complete project planning in relation to the drive technology.
- Application programming – for the optimum use of your drive technology. Tailor-made drive component software for your application enables you to make the most of all the advantages and functions.
- Startup – for maximum reliability and efficiency. We start up all your drive technology, naturally taking account of current safety regulations, and set all parameters to optimum values. We are also happy for you to look over our shoulder to learn at the same time.
OPERATION
The usage phase is typically the longest phase in the life cycle of your machine or system and has a significant impact on the overall life cycle costs. We want to assist you in minimizing these costs from the outset and raising the availability and productivity of your system on a continuous basis. You can take advantage of our remote service, repair services including Pick-Up and Delivery Service as well as energy consulting to support your energy management system.
Optimum services in this phase:
- Production support – from our experts in your production start-up phase to enable you to identify problems early. Where necessary, we will train your staff or provide process optimization support. We will supervise the drive technology during the startup phase, train your staff if necessary, and help you optimize your process sequences.
- Remote service – remote access enables us to diagnose the current status of your drive technology and make an appropriate fault evaluation. All you need is an on-site computer with an internet connection.
- Repairs – should it be necessary, even on products from other manufacturers. Emergency repairs, functional repairs and repairs all the way to as-new repair work with a 24-month guarantee on the complete drive. And if things have to be done in a hurry, ask about our rush order repairs and our on-site service.
- Inspection & Maintenance – to increase your operational reliability and system availability, e.g. using endoscopy for gear unit diagnostics or using oil check for analyzing gearmotor oil. We will happily check your entire drive technology in an existing system and give you a 12-month liability for defects on all drive components we have checked and found to be in working order. Simply ask about the SEW Quick check.
- Spare parts service – in 95 percent of cases we dispatch on the same day. We ensure immediate availability and provision of original SEW-EURODRIVE spare parts. This can also be done through the Online Support customer portal.
- Pick-Up and Delivery-Service – ensures the fast pick-up and delivery of your drive technology. Our service experts will also provide support with the disassembly and reassembly of the drive components. We can also take over the entire transport logistics – ask us about the Pick-Up Box!
- Express Assembly – when you urgently need replacement or new gearmotors and electronic products. We are generally able to assemble and deliver on the same day as the order is placed, thereby ensuring greater process reliability and shorter downtime.
- Condition monitoring – based on systematic determination of the condition of the drive and automation technology. This minimizes your production downtime e.g. with brakes diagnosis or SmartCheck vibration sensor. You receive entire concepts, from initial consulting and designing of the optimal analysis method all the way through to installation and diagnostics.
- 24h Service Hotline – staffed by trained technicians and engineers. To provide technical information, arrange rush orders for repairs, or handle express assembly and replacement part dispatch.
- Energy management – to help you optimize the energy efficiency of your machinery and systems. Reduce your energy costs and benefit from an energy report that proves the success of your energy management system.
MODERNIZATION
The service life of machines and systems is increasing on a continuous basis and this brings with it a great deal of change, such is with regard to legal provisions and normative specifications but also in terms of the requirements relating to productivity, system availability, performance and parts availability. Sooner or later, you will be faced with the decision of whether to modernize your system, or individual parts of it. While such a step can yield significant economic benefits, we appreciate that system modernization is a highly demanding task from an engineering and service perspective. That is why we can support you with this endeavor in close cooperation.
Optimum services in this phase:
- Retrofit – updates your system with state-of-the-art technology. Boost your productivity and energy efficiency, cut your maintenance costs, benefit from long-term parts availability. Everything from a single source – our retrofit service offers personal consulting and engineering, state-of-the-art drive technology, programming and visualization, along with complete installation and startup.
Visit us in Hall 15, stand F09 to find out more
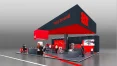
Visit us at our extended stand F09 directly next to the main stand F12.
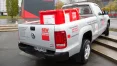
Even if your system is functioning flawlessly, it is helpful to have a partner at your side, who can advise you on such matters as process optimization, savings potential, pick-up services and much more besides… Visit us to find out more about our Life Cycle Services: Here in Hall 15 at our extended stand F09.